Houses
Residential facilities are the core part of activity for Wiazar-System. We focus on quality and precision of our prefabricated elements. We are aware of the importance of warmth and safety for of customers, so we make every effort to make these available to them. Choice of nail plates and sections of solid wood is not a discretionary design method, as it is in the case of a traditional timber roof truss developed by designers in studios and frequently manufactured in an altered form by carpenters on the construction site.
The quite common use of practised schemes resulted in widespread use of wooden cross-sections for traditional timber roof trusses with cross-sections that are too large and not related to actual tension they should be exposed to. This generates costs and increases the weight of the structure.
In the case of prefabricated trusses, the entire production process begins in the design studio where a skilled constructor uses specialist licensed software for such products. The constructor makes static and strength calculations to adapt the attic trusses to the required spacing and span. At this stage one might focus on every single truss so as to make it adapted to the investor’s needs in terms of width and height of the room, taking into account the strength conditions. The design provides an opportunity of economical distribution of material for typical or individual construction solutions. Such a project prepared in the form of an electronic file is transferred to numerically controlled saws that cut the previously impregnated lumber under the supervision of their operators. All of the elements of this system along with galvanised metal fasteners in the form of nail plates are manually or laser-dismantled in line with the guidelines of a given project. The last step of such production process is to press the plates into wooden elements using hydraulic presses with adjustable compression up to 40 t.

The entire production is planned in detail with an emphasis
on maintaining the highest quality at a reasonable price,
because it is customer satisfaction that we care about most.

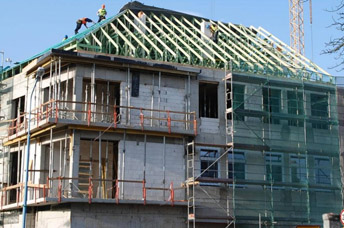
- Spans up to 30 m between supports.
- Savings resulting from the lack of the need for knee walls and mandrels.
- It is possible to design open spaces for attic or attic without major costs.